Преимущества газопламенного напыления
- Сверхзвуковое (высокоскоростное) газопламенное напыление металла можно проводить на деталях различной конфигурации поверхности и степени сложности.
- В качестве напыляемого материала можно использовать металлы и полимеры с низкой пластичностью.
- Простота в восстановлении нанесенного покрытия.
- Отсутствие деформации поверхности при напылении.
Также очень широко сейчас применяется технология высокоскоростного (сверхзвукового) газопламенного напыления (HVOF). В данном способе при нанесении порошкового материала используются сверхзвуковые скорости. Изменение скоростного режима привело к тому, что данный способ нецелесообразно применять вручную, так как отдачу невозможно контролировать на таких скоростях. Поэтому для нанесения напыления требуются автоматизированные установки, которые способны нанести однородный слой нужной толщины и при этом выдержать отдачу. Увеличение скорости также повлияло на напыляемый материал. В данной технологии активно используют сплавы железа и никеля, а также карбиды.
Данные методы газопламенного напыления широко используются при восстановлении геометрической формы элементов различного оборудования, валов двигателей, нестандартных деталей и др. Также в спектр применения входит нанесение износоустойчивых и антикоррозийных покрытий, увеличивающих срок службы различных материалов.
Особенности и назначение плазменного напыления
Особенность покрытия — пластинчатая зернистая структура, возникающая в результате термической диффузии мелких частиц.
Стадии плазменного напыления металла:
- Ионизация частиц.
- Распыление.
- Осаждение.
- Затвердевание.
На каждом из этапов необходимо проводить контроль температуры и скорости движения напыляемых частиц.
Осаждение представляет собой совокупность двух, одновременно протекающих процессов – химической связи, которая активируется вследствие высоких температур в зоне обработки, и механических взаимодействий, обусловленных повышенной кинетической энергией частиц напыляемого металла. Дополнительным интенсифицирующим фактором считается наличие промежуточной среды – газа/жидкости — молекулы которой ускоряют и стабилизируют процесс металлизации. При этом образуются дополнительные соединения, улучшающие качество напылённого слоя. Например, азот формирует высокотвёрдые нитриды металлов, гелий предотвращает окисление поверхности, а медь улучшает условия трения.
Плазменное напыление металлов часто применяется для восстановления изношенных стальных деталей
Технология газопламенного напыления
Технология проволочного газопламенного напыления, которую наиболее широко используют в промышленности, должна отвечать следующим требованиям.
Сжатый воздух, используемый для распыления расплавленной проволоки, должен быть сухим и не содержать масла. Давление сжатого воздуха должно быть не менее 0,4 МПа (4 физических атмосферы).
Перед напылением необходимо тщательно осмотреть поверхность. Если в результате осмотра установлено, что на ней имеются следы влаги, окисная пленка, окалина и другие загрязнения, необходима вторичная обдувка абразивными материалами. Первый слой покрытия напыляют в течение 4 часов после обдувки. Окончательное напыление покрытия до требуемой толщины должно быть проведено не более чем через 8 часов после предварительной обработки.
Зажигать горелку и выводить ее на рабочий режим необходимо вдали от напыляемой поверхности. Расстояние от горелки до поверхности детали обычно составляет 75…250 мм. Выбор величины этого расстояния зависит от напыляемого материала и диаметра проволоки, а также от свойств напыляемого покрытия. При очень малом расстоянии может возникнуть опасность коробления основы под действием термических напряжений. Когда же расстояние слишком большое, температура летящих частиц снижается, что приводит к образованию рыхлого покрытия и уменьшению прочности сцепления с основой, что может вызвать отделение покрытия от основы.
При порошковом напылении керамики расстояние от среза сопла горелки до основы составляет 150…200 мм, а в случае напыления пруткового материала это расстояние около 75 мм.
Наибольшая деформация напыляемых частиц при соударении с поверхностью основы происходит, если горелка установлена относительно нее под углом 90°. Когда невозможно обеспечить этот угол, покрытие получается с несколько худшими характеристиками. Допустимый угол наклона горелки, при котором можно наносить покрытие, составляет не менее 45°.
При напылении режим работы горелки, скорость перемещения и расстояние напыления должны поддерживаться постоянными. Обычно скорость перемещения горелки или основы при напылении на плоские поверхности составляет от 10 до 25 м/мин, а шаг перемещения горелки – 6…12 мм.
В случае перегрева поверхности основы при напылении происходит снижение прочности сцепления покрытия. Как правило, температура поверхности напыляемой детали не должна превышать 260 °С. Для контроля температуры основы можно воспользоваться, например, термопарами, термокарандашами или термокрасками, которые наносят на деталь в непосредственной близости от места напыления. Для предотвращения перегрева при напылении обрабатываемую основу можно охлаждать воздухом.
При температуре напыляемой поверхности, близкой к 0 °С и ниже, проводить напыление не рекомендуется, так как покрытие может отслоиться. Для того чтобы покрытие не растрескалось, необходимо предварительно нагреть основу до температуры 100…120 °С. От способа предварительной обработки основы в значительной степени зависит толщина наносимого покрытия. Нарезка резьбы на напыляемой поверхности позволяет наносить более толстые покрытия по сравнению с подготовкой поверхности обдувкой абразивными материалами.
При механическом перемещении напыляемого изделия или горелки процесс напыления принимает более устойчивый характер и покрытие можно получить более однородным. Для напыления на валы часто используют токарные станки. Обычно в этих случаях горелку устанавливают на суппорте. После напыления на этом же станке, не вынимая детали, можно произвести ее обточку или шлифование. При напылении покрытий на большие партии изделий процесс напыления желательно автоматизировать.
Покрытие, полученное после напыления, по своей структуре является в значительной степени пористым. Пористость его можно в некоторых случаях эффективно использовать. Заполнять поры можно путем нанесения на покрытие слоя краски, пропиткой покрытия специальными составами или проплавлением его, если оно получено из самофлюсующихся сплавов. Для улучшения механических свойств и термостойкости покрытия его можно подвергнуть также термической обработке. Однако наиболее широкое применение находят плотные покрытия.
Дополнительная комплектация
- горелки для внутреннего напыления (600, 1000 и 1500 мм) (рис. 11).
- соединительные газовые рукава для горелки внутреннего напыления.

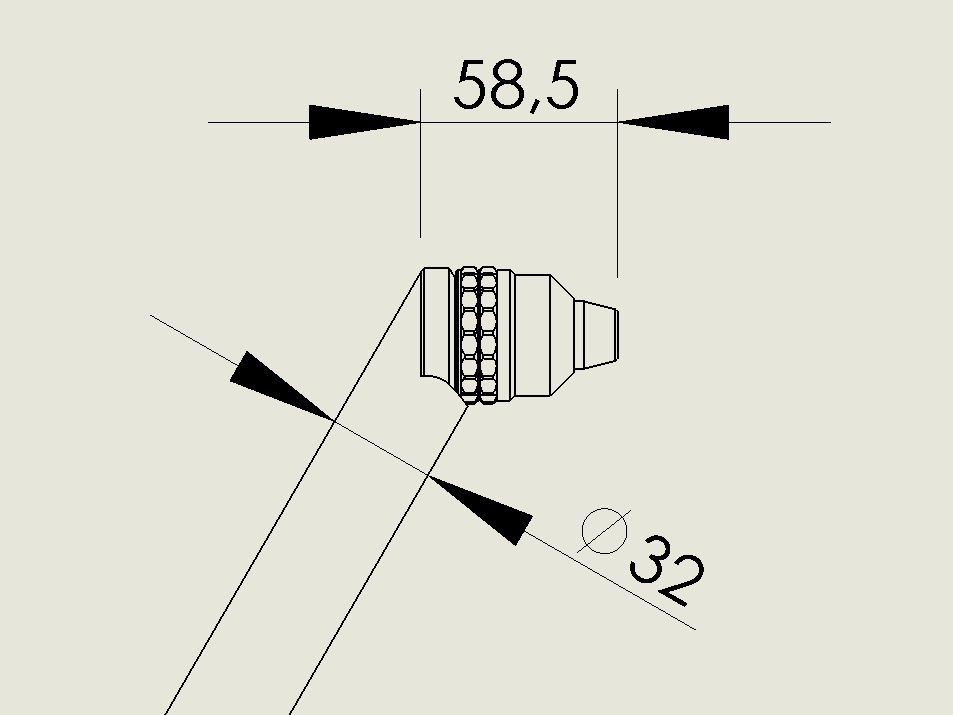
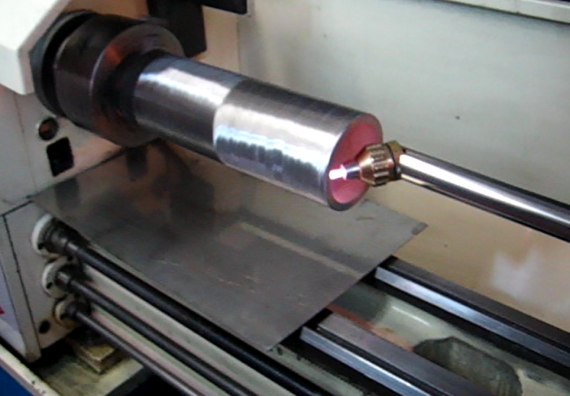
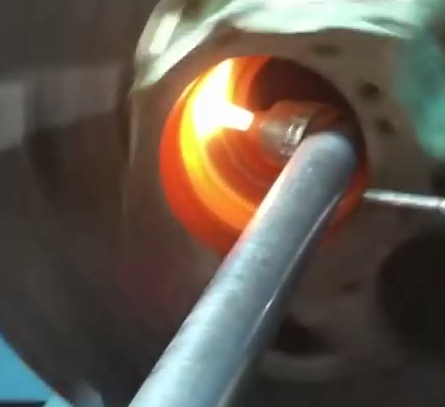
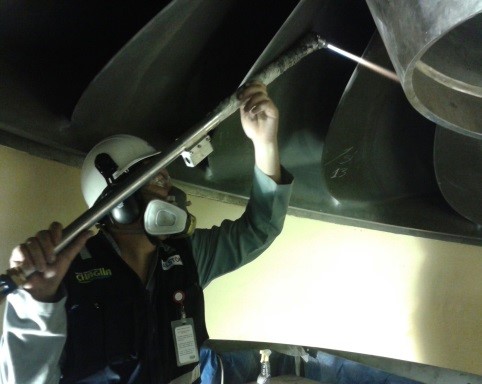
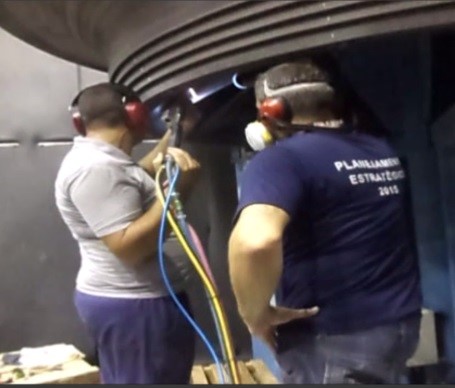
Установка HVOF-TERMIKA-3 отличается от аналогов удобством, простотой обслуживания, компактностью и надежностью и обеспечивают напыление тех же покрытий, что и системы, которые стоят в десятки раз дороже. Установка может использоваться как на крупных, так и небольших предприятиях, связанных с упрочнением или восстановлением деталей.
«Плазмацентр» предлагает
- услуги по восстановлению деталей, нанесению покрытий, напылению в вакууме, микроплазменному напылению, электроискровому легированию, плазменной обработке, аттестации покрытий, напылению нитрида титана, ремонту валов, покрытию от коррозии, нанесению защитного покрытия, упрочнению деталей;
- поставка оборудования для процессов финишного плазменного упрочнения, сварки, пайки, наплавки, напыления (например, газотермического, газопламенного, микроплазменного, высокоскоростного и детонационного напыления), электроискрового легирования, приборов контроля, порошковых дозаторов, плазмотронов и другого оборудования;
- поставка расходных материалов, таких как сварочная проволока, электроды, прутки для сварки, порошки для напыления, порошки для наплавки, порошки для аддитивных технологий, проволока для наплавки и другие материалы для процессов сварки, наплавки, напыления, аддитивных технологий и упрочнения;
- проведение НИОКР в области инженерии поверхности, трибологии покрытий, плазменных методов обработки, выбора оптимальных покрытий и методов их нанесения;
- обучение, консалтинг в области наплавки, напыления, упрочнения, модификации, закалки.
Наши менеджеры подробно расскажут об имеющихся у нас технологиях нанесения покрытий, упрочнения, восстановления, придания свойств поверхности, а также о стоимости услуг компании.
Нанесение детонационных покрытий
Метод детонационного нанесения покрытий основан на высокоскоростном ударном взаимодействии нагретых до высоких температур частиц порошка напыленного материала с подложкой (рис. 5).
Рис. 5. Схема детонационной установки с внутренним смесеобразованием: 1 – клапан подачи ацетилена; 2 –клапан подачи азота; 3 – канал подачи порошка; 4 – свеча зажигания; 5 – ствол пушки; 6 – клапан подачи кислорода; 7 – мишень
Детонационная установка с внутренними смесеобразователями представляет собой водоохлаждаемый ствол длиной 1…1,8 м с внутренним диаметром от 10 до 40 мм. В ствол подается смесь кислорода и ацетилена вместе с порцией порошка. Взрываемая газовая смесь воспламеняется при помощи электрического импульса, и детонационная волна перемещается по стволу, ускоряя и нагревая порошок. Частицы порошка ускоряются до скорости 500…1000 м/с и ударяются в деталь, образуя пятно напыленного покрытия. Затем ствол очищается азотом, и процесс повторяется. Процесс напыления осуществляется циклически (4…10 циклов в секунду). Детонационные покрытия обеспечивают повышение эксплуатационных свойств и ресурса работы узлов, машин и механизмов, восстанавливают изношенные детали (до 1 мм на сторону).
Материалы покрытий:
- металлы и их оксиды, карбиды, бориды, нитриды;
- твердые сплавы;
- композитные порошки.
Высокоскоростное газопламенное напыление (HVOF «High Velocity Oxygen Fuel Spraying»)
Высокоскоростное газопламенное напыление по праву считается наиболее современной из технологий напыления. В странах Европы и Северной Америки высокоскоростное напыление практически вытеснило гальванику и методы вакуумного напыления во многих отраслях. Твердосплавные покрытия, нанесенные методами высокоскоростного напыления, по всем статьям превосходят гальванические покрытия, процесс создания которых признан чрезвычайно канцерогенным.
В начале 80-х годов прошлого века появились установки высокоскоростного напыления, более простые по конструкции и основанные на классической схеме жидкостного реактивного двигателя, со скоростью газового потока более 2000 м/с.
Плотность покрытий достигает при этом 99 %. В качестве наносимого материала используют порошки карбидов, металлокарбидов, сплавов на основе Ni, Cu и др. Для увеличения скорости частиц увеличивают скорость истечения продуктов сгорания путем повышения давления в камере сгорания до 1,5 МПа, а в конструкцию горелки вводят сопло Лаваля. На рис. 3 представлена схема распылителя системы высокоскоростного напыления.
В результате порошкового напыления образуется надежное, долговечное покрытие, обладающее отличными эксплуатационными свойствами. В том числе устойчивостью к коррозии, истиранию, ударам и другим внешним воздействиям. Оно продлевает срок службы изделий на десятки лет. При этом стоимость такого защитного покрытия гораздо ниже, чем аналогичного гальванического.
Рис. 3. Схема высокоскоростного напыления порошка: 1 – канал осевой подачи порошка; 2 – подача кислорода; 3 – подача топлива; 4 – канал радиальной подачи порошка; 5 – ствол горелки; 6 – сопло Лаваля; 7 – струя разогретого порошка; 8 – напыляемая поверхность
Газопламенное напыление
Газопламенное напыление в зависимости от состояния напыляемого материала может быть трех типов: напыление проволокой, прутком или порошком (рисунок 1.12).
Схема газопламенного напыления
Рисунок 1.12 – Схема газопламенного напыления:
П – покрытие;
С – струя напыляемого материала и продуктов сгорания газов.
Напыляемый материал, имеющий форму прутка или проволоки, подают через центральное отверстие горелки и расплавляют пламенем горючей смеси. Расплавленные частицы металла подхватываются струёй сжатого воздуха и в мелкораспыленном виде направляются на поверхность изделия. Проволока подаётся с заданной скоростью роликами, приводимыми в движение встроенной в горелку воздушной турбиной, работающей на сжатом воздухе, используемом при напылении, или электродвигателем через редуктор.
Для напыления обычно используют проволоку диаметром не более 3 мм, однако при напылении легкоплавкими металлами (алюминий, цинк и т. п.) в интересах повышения производительности процесса допускается использование проволоки диаметром 5-7 мм. В качестве горючего газа в большинстве случаев используют ацетилен, можно также применять пропан и водород, а в качестве окислителя – кислород.
При газопламенном способе напыление осуществляется в основном теми материалами, температура плавления которых ниже температуры пламени. После напыления иногда проводят оплавление покрытия, которому, в частности, подвергают покрытия, напыленные самофлюсующимися сплавами на никелевой и кобальтовой основе с добавлением в них в качестве флюсующих добавок бора и кремния.
Оплавление обеспечивает получение плотного покрытия, практически без пористости. Технология газопламенного напыления довольно проста, а стоимость оборудования и затраты на эксплуатацию низкие, в связи с этим данный способ находит широкое применение в практике. Процесс газопламенного напыления хорошо поддаётся автоматизации.
Краткие характеристики покрытия:
- Пористость покрытия, 5–12%;
- Прочность сцепления покрытия с основой (адгезия), 2,5 –5,0 кг/ мм2 ;
- Толщина напыленного слоя, 0,5 –10 мм.
Технология процесса напыления
Исходный материал подается в столб плазмы в форме порошка или проволоки. Ионизированные газы высвобождают активные молекулы газов, некоторые из которых (например, водород) дополнительно поднимают температуру внутри плазменного столба, ускоряя процесс превращения молекул исходной заготовки в парообразное состояние. В результате ускоряется оседание движущихся частиц на подложку. Ионизация возможна не только из газа, но и из жидкости, испаряющейся в столбе дуги.
Напыляющие порошки разнообразят состав и свойства покрытий, поскольку в мелкодисперсное состояние может быть переработан широкий спектр металлов.
Варианты плазменной металлизации
Для нанесения на металлическую поверхность некоторого слоя напыления в условиях высокотемпературной плазменной среды в качестве формирующих покрытий используют не только порошковые составы. В зависимости от того, какими свойствами должна обладать обработанная поверхность, используют следующие особенности плазменной металлизации:
- Наплавление высокоуглеродистой или легированной проволокой под флюсом. Для восстановления поверхностей используют наплавку в установках стержневым или пластинчатым электродом.
- Наплавка по порошковому слою под флюсом используется для реставрации деталей с обширными деформациями по окружности с толщиной слоя более 2 мм.
- Установки для напыления пропускают в качестве плазмообразующих газов аргон, азот, водород, гелий либо их смеси. Необходимо обеспечить отсутствие кислорода, чтобы исключить окисление наплавляемых покрытий.
Наиболее часто этот вид обработки используют для восстановления различных деталей при ремонте автомобильных двигателей. Так, при помощи диффузной металлизации удается восстановить отверстия коренных опор в блоках цилиндров (распространенная поломка), устранить износ головок цилиндров, реставрировать поршни из алюминиевого сплава, коленчатые валы из высокопрочного чугуна, ролики, катки.
При использовании ионно-плазменного напыления значительно возрастает износостойкость сложных узлов оборудования, механизмов и установок. Диффузная металлизация – это эффективный метод реставрации изношенного и усталого металла, а также оптимальный процесс для задания металлическим поверхностям необходимых прочностных и эксплуатационных характеристик.
Где используют плазменную металлизацию
Поскольку напыляемым материалом может служить практически любой сплав или металл, ионно-плазменное напыление широко используют в различных отраслях промышленности, а также для проведения ремонтно-восстановительных работ. Любой металл в виде порошков подается в плазменные установки, где под воздействием высокотемпературной плазмы расплавляется и проникает в обрабатываемую металлическую поверхность в виде тонкого слоя напыления. Сферы применения диффузной металлизации:
- детали для авиационной, космической и ракетной промышленности;
- машиностроительное оборудование и энергетическая отрасль;
- металлургическая и химическая отрасль промышленности;
- нефтедобывающая, нефтеперерабатывающая и угольная отрасль;
- транспортная сфера и производство приборов;
- ремонт и реставрация машин, оборудования, изношенных деталей.
Когда струя плазмы и порошков проходит по электродуге и осаживается на обрабатываемой поверхности, образованный слой приобретает важные качественные и эксплуатационные характеристики:
- жаростойкость;
- жаропрочность;
- коррозийную устойчивость;
- электроизоляцию;
- теплоизоляцию;
- эрозийную прочность;
- кавитационную защиту;
- магнитные характеристики;
- полупроводниковые свойства.
Технологический процесс вакуумной металлизации
Рассматриваемый метод обработки деталей применяется достаточно давно. Вакуумная металлизация – процесс, основанный на испарении и выпадении конденсата материала на подложку. Среди особенностей данного процесса следует отметить нижеприведенные моменты:
- Универсальность и высокая эффективность метода определяет его большое распространение. В будущем ожидается более обширное применение процесса металлизации полимерных и других материалов. Развитие рассматриваемого метода обработки связывают с совершенствованием используемого оборудования. Так современные вакуумные установить позволяют автоматизировать процедуру металлизации деталей, повысить качество получаемых поверхностей, снизить себестоимость получаемых изделий. Единственное препятствие на пути развития данной отрасли – высокая стоимость современного оборудования и возникающие сложности при его установке, использовании и обслуживании.
- Технологический процесс вакуумной металлизации достаточно сложен, на результате отражается условие проведения каждого этапа. При нагреве материала, который должен стать будущим покрытием, он претерпевает большое количество изменений. Примером можно назвать то, что изначально покрытие испаряется, затем происходит адсорбция, после чего выпадение конденсата и кристаллизация для закрепления слоя на поверхности.
- На качество получаемого результата оказывает воздействие достаточно большое количество факторов, среди которых отметим физико-химические качества подложки, выдерживаемые условия проведения металлизации.
- Образование напыляемого покрытия при металлизации происходит в два основных этапа: перенос энергии и массы от источника к поверхности и их распределение по всей подложке.
Оборудование для вакуумной металлизации
Установка для вакуумной металлизации
Технология вакуумной металлизации подходит для обработки самых различных деталей. В качестве примера можно привести рулонные материалы из пластика или пластмассы.
Типовая технология состоит из нескольких основных этапов:
Подготовка детали к проводимому процессу. Среди требований, которые предъявляются к детали можно отметить отсутствие острых кромок и скрытых участков от прямолинейного попадания конденсата. Вакуумная металлизация пластмасс или других материалов возможна только в том случае, если фора заготовки не сложная. Обезжиривание и сушка. Некоторые материалы могут содержать большое количество адсорбированной влаги, к примеру, полимеры. Сушка проводится при температуре около 80 градусов Цельсия, время выдержки составляет 3 часа. Обезжиривание уже проводится в вакуумной камере на подготовительном этапе. Технология обезжиривания предусматривает разматывание рулона и воздействие тлеющего разряда. Как показывают результаты проведенных исследований, выполнение отжига на стадии подготовки полимеров благоприятно сказывается на структуре рассматриваемого материала, так как существенно снижается показатель внутреннего напряжения. Вакуумная рулонная металлизация должна проводится с исключением вероятности образования складок на этапе подготовке заготовки, так как их можно назвать дефектов. Этап активационной обработки поверхности. Вакуумная металлизация пластика и других материалов предусматривает активацию поверхности. При этом могут использоваться самые различные методы активации, выбор которых зависит от качеств самого материала. Данный процесс предназначен для повышения показателя адгезии поверхности. Нанесение вещества на поверхность. В большинстве случае вакуумная металлизация алюминия или другого сплава проходит при применении резистивного метода испарения при условии воздействия температуры. Вольфрамовая технология испарения применяется намного реже, так как предусматривает нагрев среды до небольшой температуры, в результате чего испаритель разрушается за минимальные сроки. Заключительный этап касается контроля качества металлизации. Если наносимый слой носит декоративный характер, то в большинстве случаев контроль качества заключается в регистрации оптических свойств
Кроме этого уделяется внимание равномерности напыления, прочности соединения поверхностного слоя и структуры. Пример получаемого вакуумной металлизацией изделия. Пример получаемого вакуумной металлизацией изделия
Пример получаемого вакуумной металлизацией изделия
Результат вакуумной металлизации
Технология вакуумной металлизации пластмасс и других материалов сложна, для получения качественной поверхности нужно соблюдать все условия обработки.
Какое оснащение применяется для диффузного напыления
Для совершения напыления ионами металла используется техническая плазма высокой температуры – совокупность множества квантовых частиц света, положительных ионов, нейтральных элементов, электронного газа.
Для того, чтоб совершить плазменную ионизацию металлоконструкции, применяется специфическое оснащение – плазменная аппаратура.
Как правило, применяется дуговой, импульсный либо искровой электрический разряд.
Чтоб все это реализовать, вам надобно воспользоваться:
- Высокочастотным генератором (или сварочным модификатором) для создания разряда.
- Герметизированной камерой (в ней вмещаются элементы для обработки основания диффузионным напылением).
- Емкостью для газа. Под влиянием электроразряда происходит ионизация элементов.
- Аппаратом для давления газа (годится вакуумное или насосное оборудование).
- Системой для изменения тока, давления, напряжения и увеличения или уменьшения толщины поверхности металла.
Порядок плазменной ионизации происходит в следующем порядке:
- Фиксация детали в герметизированной камере, и формирование электрического разряда.
- Рабочая атмосфера накачивается давлением и частицами порошка (получается плазма высокой температуры, переносящая порошковые элементы на основание обрабатываемого изделия).
- При вакуумном напылении, в условии инертного газа или низком давлении возможно ускорение движения элементов, вследствие чего получается более плотное и с хорошей сцепляемостью покрытие.