Функции гранулированных флюсовых смесей
Каждый тип флюса должен выполнять четыре функции:
Стабилизация сварочного процесса
Правильные флюсовые смеси оказывают самое благоприятное воздействие на электрическую дугу: сварка под слоем флюса создает самую комфортную среду для горения дуги – электрического разряда между электродом и краем изделия. Обычно расстояние между полюсами дуги составляет около 5-ти мм.
Если в гранулированной смеси флюса имеются специальные вещества, разряд будет проходить более устойчиво. А это делает возможной сварку не только на постоянном токе, но и на переменном. Кроме этого такая стабилизация дуги помогает применять большее число разных режимов сварки.
Изоляция газового облака
Варианты керамического флюса.
Газовое облако должно быть в любом случае непроницаемым, без него металлы не смогут расплавляться в сварочной ванне. Чтобы порошковая флюсовая смесь нормально справлялась с данной задачей, нужно подсчитать максимально точно дозировку порошка на линии шва.
Чем мельче гранулы флюса и чем они плотнее, тем лучше происходит изоляция газового облака. Но совсем мелкой смесь тоже не должна быть, иначе плотность насыпки на поверхности шва будет негативно влиять на его правильное формирование.
Помимо размера гранул смеси на ее изолирующие свойства влияет масса насыпки. Для ее определения существуют специальные таблицы, с помощью которых можно очень точно определить дозу подачи флюса в рабочую сварочную зону.
Функция легирования
Сварочный шов формируется в результате действия высоких температур плавления и физическому взаимодействию металлов – основного и присадочного. Химический состав шва обусловлен видом применяемых материалов. Но под влиянием дуги некоторые нужные и полезные элементы могут выгорать или осаждаться в шлаковых массах.
Чтобы полноценно заменить их, в определенные виды флюсов добавляют специальные легирующие добавки, которые обогащают металлы, образующие шов. Кроме того, такие добавки тормозят нежелательный процесс – переход в шлак марганца и кремния. Если легирование используется, параллельно применяют специализированную присадочную проволоку.
Формирование поверхности
Режимы сварки меди под флюсом.
Прекрасным примером может служить технология сварки под флюсом с применением так называемых «длинных» порошков. Речь о сварке толстых краев металлов на большой силе тока. Для таких условий самым оптимальным вариантом будет использование флюсовые смеси с высокой вязкостью, которая делает процесс остывания медленным и постепенным.
Такая постепенность дает возможность образоваться кристаллической решетке с гладко-чешуйчатой структурой.
В ситуациях «наоборот» – при флюсовой сварке с малыми токами сильная вязкость вовсе не нужна. В таких случаях применяются «короткие» флюсовые смеси, которые при остывании мгновенно превращаются в твердое вещество. Режимы сварки под флюсом – моменты тонкие и важные, от них зависит и качество шва, и форма его поверхности.
Автоматическая сварка тавровых и нахлёсточных соединений под флюсом
Автоматическая сварка тавровых и нахлёсточных соединений, в зависимости от
конструктивных особенностей свариваемых изделий, осуществляется вертикальным
электродом, при положении сварного соединения «в лодочку» (схема а)
на рисунке ниже), или наклонным электродом в том случае, когда один из листов
или оба листа имеют горизонтальное положение (схема б) на рисунке ниже:
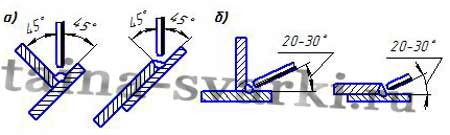
При этом сварка может выполняться с односторонней разделкой кромок, с двухсторонней,
или, вообще без разделки и зависит это от толщины свариваемого металла (см.
рисунок ниже), а также от требований, предъявляемых к металлоконструкции и условий
её эксплуатации.
Если зазор между свариваемыми деталями не превышает 1мм, сварка в «лодочку»
осуществляется на весу и дополнительные приспособления (металлические подкладки
и флюсовую подушку) не используют. При большом зазоре, превышающем 1мм, применяют
сварку на медных или стальных подкладках, или на флюсовой подушке. Возможна
заделка зазора асбестовыми уплотнениями, или выполнение подварочного шва с обратной
стороны.
Сварка «в лодочку» позволяет равномерно проварить кромки свариваемого
изделия и получить качественный сварной шов большого сечения за один проход.
Но для того, чтобы осуществить такую сварку, необходимы специальные кантователи,
на которые устанавливают сварное соединение.
При автоматической сварке под флюсом тавровых или нахлёсточных соединений наклонным
электродом, он находится под углом 20-30° к горизонту. Такой способ сварки не
позволяет получить сварные швы с катетом более 16мм, что является его недостатком.
Поэтому часто приходится применять многослойную сварку. Приблизительные режимы
автоматической сварки тавровых и нахлёсточных соединений «в лодочку»,
выполняемой сварочной проволокой диаметром 5мм, можно выбрать по таблице:
Катет шва, мм | Сила тока, А | Напряжение дуги, В | Скорость сварки, м/ч | Скорость подачи проволоки, м/ч |
5 | 600-650 | 34-36 | 58,0 | 60,7 |
6 | 650-700 | 34-36 | 47,0 | 67,3 |
7 | 700-730 | 34-36 | 38,5 | 71,1 |
8 | 700-750 | 34-36 | 32,0 | 73,5 |
9 | 750-780 | 34-36 | 27,5 | 78,0 |
10 | 750-800 | 34-36 | 24,0 | 81,3 |
12 | 850-900 | 34-36 | 19,0 | 95,3 |
14 | 900-950 | 36-38 | 16,0 | 103,0 |
16 | 950-1000 | 38-40 | 13,0 | 111,0 |
Дополнительную информацию о выборе режимов сварки, в зависимости от свариваемого
материала и его толщины, можно узнать на странице: «Режимы
для автоматической сварки под флюсом».
Дополнительные материалы по теме:
Плавленые |
Технология |
Технология автоматической сварки под флюсом
Подготовительные операции: очистка места соединения от ржавчины, грязи и других посторонних включений металлической щеткой и шлифовальным кругом. Процесс идёт автоматически, оператор задаёт только один из режимов, перечисленных выше.
Флюс насыпают слоем 50-60 мм. Дуга скрыта под массой порошка и горит в его жидкой среде. Этот метод ведётся чаще на токе высокой плотности, поэтому используют автоматы с постоянной скоростью подачи проволоки. Она извлекается из бобины автоматически, как и флюс, который предварительно засыпают в специальный резервуар.
Примерная стоимость сварочного флюса на Яндекс.маркет
Особенности технологического процесса, материалы
Сварочная дуга горит в облаке газа, образованном плавлением и испарением флюса. Когда она гаснет, расплавленный порошок остывает и образует шлаковую корку. Его засыпают перед дугой слоем шириной 40-80 мм и длиной 40-100 мм. Неиспользованный материал отсасывается обратно в бункер и запускается повторно.
В промышленных масштабах сваривают проволокой или ленточными электродами. В качестве флюсов выступают искусственные силикаты: закись марганца, окиси магния, алюминия, кальция.
Недостаток – отсутствие возможности сваривать вертикальные швы.
Оборудование: принцип действия
Для работы этим методом существует два типа аппаратов:
- Электродная проволока подаётся с постоянной скоростью и не зависит от напряжения на дуге.
- Напряжение на дуге регулируется автоматически, от него зависит скорость подачи электродной проволоки.
На установках с постоянной скоростью сварочный ток подбирают в соответствии со временем подачи гибкого электрода, напряжение – изменением внешней характеристики источника питания.
Примерная стоимость сварочных аппаратов на Яндекс.маркет
Настройки остальных параметров процесса – вылета электрода и высоты флюса – одинаковы для обоих типов аппаратов и зависят от конструкционных особенностей самих установок.
Режимы автоматической сварки и основные параметры
Технические условия (ТУ) для сварки различных изделий содержат всю информацию, необходимую для работы мастера. При отсутствии таких данных специалист подбирает нужный режим сварки, проводя эксперименты на заготовках, выполненных из аналогичного сплава.
Используется несколько различных методов создания соединений. Однако при применении автоматизированного процесса отдают предпочтение электродуговой сварке с защитой флюсом. Специалисты называют ее самой эффективной. В данной статье мы затронем режимы автоматической сварки и расчет основных параметров их проведения.
Примечание. Сварка под флюсом в автоматическом режиме целесообразна, если толщина обрабатываемого изделия (мм) в пределах 5–50.
Основные особенности процесса:
- Необходимо аккуратно и скрупулезно проводить обработку краев шва. Причина заключается в пористой структуре разъема, из-за чего часто образуются трещины, причем это относится ко всему шву.
- Проводить сварку следует сразу после обработки краев.
- Требования к материалам заготовки и электродов достаточно высоки.
Важными параметрами сварки являются:
-
Сварочный ток (I). Глубина провара во многом зависит от величины тока, проходящего через дугу. На нее оказывает влияние состав сплава, толщина заготовки, а также рисунок предстоящей сварки.
Для перераспределения тепла между заготовкой и электродом (плавящимся) чрезвычайно важна полярность электрического тока: прямая используется специалистами для того, чтобы повысить количество наплавляемого материала в шве. Однако она приводит к разбрызгиванию металла из сварочной ванны и снижает стойкость горения дуги.
Но чаще используют обратную полярность. Ее предпочитают для работы под защитой флюсом с большинством металлов, исключение составляет только алюминий.
-
Скорость сварки (V). Правильность формы сечения соединения во многом зависит от того, насколько оптимальным был выбор скорости сварки. Она оказывает прямое влияние на время прохождения сварочных процессов (металлургических и тепловых), а также на срок жидкого состояния ванны. Обратное влияние скорость оказывает на погонную энергию и расход тепла.
С изменением показателя скорости соединения меняются коэффициент формы сечения, ширина и глубина шва.
- Напряжение сварочного тока (U). Напряжение влияет на размер контактного пятна дуги при ее соприкосновении с металлом. Увеличение приводит к его возрастанию. Низкое напряжение приводит к созданию вогнутого валика шва, не имеющего усиления. Кроме того происходит появление подрезов по линии шва. Высокое напряжение способствует узкой зоне проплавки и создает усиление шва.
-
Диаметр электрода (проволоки), (∅). Плотность тока обратно пропорциональна диаметру электродной проволоки при определенном токе.
Плотность тока увеличивается с уменьшением диаметра электрода. Возрастая, плотность тока уменьшает коэффициент формы соединения.
Процесс сварки
Когда детали свариваются с использованием флюса, горение дуги происходит с помощью оригинального гранулированного порошка. Высокая температура вызывает плавление электрода и окружающих его гранул. В результате появляется эластичная плёнка, которая окружает сварочную область.
Плёнка закрывает доступ кислорода к сварочной дуге. Шов получается без трещин и раковин. После остывания флюс обращается в шлак, равномерно закрывающий шов. Когда операция завершена, твёрдая корка удаляется механическим путём. Оставшийся флюс используется для проведения дальнейших операций. Такое «сыпучее одеяло» годится для проведения работ на различном оборудовании.
Сварка под флюсом различных типов сталей
Сварка конструкционных углеродистых сталей
При сварке конструкционных малоуглеродистых сталей используют флюсы марок АН-348А, ОСЦ-45, АНЦ-1 и другие в сочетании с малоуглеродистыми или марганцевыми проволоками марок Св-08А, Св-08ГА, Св-10Г2.
Сварку среднеуглеродистых сталей выполняют при пониженных режимах, что существенно сказывается на производительности, поэтому, при изготовлении конструкции из среднеуглеродистых сталей данный вид сварки не нашёл широкого распространения на практике.
Высокоуглеродистые конструкционные стали содержат 0,46-0,75% углерода и свариваемость их затруднена. Для сварных конструкций эти стали не используются и необходимость в их сваривании возникает, как правило, при ремонтных работах. В большинстве случае, ремонт выполняют методом наплавки.
Сварка низколегированных сталей
К низколегированным сталям относят группу сталей, содержащих в составе менее 5% легирующих элементов. Оценивая свариваемость сталей этой группы, можно сказать, что при сварке под флюсом их свариваемость существенно не отличается от нелегированных малоуглеродистых сталей. Но, легирующие элементы в составе стали повышают склонность сталей к росту зёрен в зоне термического влияния, а при высокой скорости охлаждения в них могут возникать неоднородные структуры закалочного характера.
Для сварки металлоконструкций из низколегированных сталей, с температурой эксплуатации до -40°C, используют высококремнистые марганцевые флюсы марок АН-22, АН-22М, АН-47, АН-67А и другие в сочетании с легированной сварочной проволокой марок Св-10НМА, Св-08ХМ, Св-08МХ и др.
Сварка среднелегированных сталей
Среднелегированными являются стали, содержащие в составе 5-10% легирующих элементов. Для современных среднелегированных сталей характерно легирование многокомпонентное, комплексное. Легирование этих сталей только одним элементом применяется редко.
К сварным конструкциям из среднелегированных сталей предъявляются требования повышенной прочности в условиях эксплуатации, а также, нередко, коррозионная стойкость, стойкость к импульсным (резко возрастающим, мгновенным) нагрузкам. Чем выше содержание легирующих элементов, тем труднее сваривать сталь.
Одной из главных проблем свариваемости среднелегированных сталей является их чувствительность к образованию горячих трещин в сварных швах, поэтому при их сварке необходимо тщательно выбирать композицию шва. Кроме этого, необходимо использовать технологические приёмы и выбирать режимы, которые позволят получить хороший коэффициент формы шва и снизить скорость охлаждения.
Для сварки конструкций из среднелегированных сталей сварка под флюсом получила достаточно широкое применение. Для такой сварки используются низкокремнистые флюсы марок Ан-15, АН-15М, АН-17М и бескремнистые марок АН-30, ОФ-6, АВ-4 и др.
Применение бескремнистых флюсов предпочтительно в тех случаях, когда к металлу шва предъявляются повышенные требования по ударной вязкости. В сочетании с вышеуказанными флюсами применяется сварочная проволока марок Св-20Х4ГМА, Св-08Х20Н9Г7Т, Св-10Х5М, Св-10ХГСН2МТ.
Сварка высоколегированных сталей
Высоколегированными считаются стали, содержащие в составе более 10% легирующих элементов. Сварка под флюсом высокоуглеродистых сталей нашла широкое применение в химической и нефтяной промышленности, где требуется высокая коррозионная стойкость сварных изделий и жаропрочность.
Своим широким применение для этих сталей сварка под флюсом получила благодаря постоянству процесса сварки и, как следствие, химической однородности металла шва
Это очень важно для высоколегированных сталей, учитывая, что даже незначительная химическая неоднородность металла шва может стать причиной образования в нём кристаллизационных трещин или заметно снизить коррозионную стойкость или жаропрочность
Сварка под флюсом способна обеспечить швы с гладкой поверхностью и плавным переходом к основному металлу, что позволяет повысить стойкость к коррозии по сравнению со сваркой электродами.
При сварке под флюсом высоколегированных сталей обычно применяют проволоку диаметром 2-3мм. При этом могут использоваться почти все марки проволоки по ГОСТ 224, а также многие марки проволоки, выпускаемые по ТУ, например, Св-12Х11НМФ, Св-12Х13, Св-10Х17Т, Св-04Х19Н9, ЭП467, ЭП235, ЭП497 и другие.
Для сварки жаропрочных высоколегированных сталей применяются фторидные флюсы марок АНФ-5, АНФ-8, АНФ-24 и бескремнистые флюсы марок АНФ-17, АНФ-22. Для сварки коррозионностойких высоколегированных сталей применяют флюсы с низким содержанием кремния марок АН-26, АНФ-14.
Разновидности автоматической сварки
Автоматический сварочный аппарат, создающий дугу подачей тока на проволоку, и защищающий сварочную ванну слоем флюса, может иметь несколько вариантов исполнения. Это могут быть станки с подвижной головкой, выполняющие ровные или шаблонные линии швов. Для трубопроводов используют неподвижные головки, под которыми изделие вращается на роликах. Тракторы сами ездят по изделию, перевозя аппарат и одновременно ведя сварку. Во всех моделях применяется плавящийся электрод (проволока ГОСТ 16130-72). За последующее время, после внедрения в промышленность этих методов, были разработаны и другие устройства, позволяющие автоматизировать сварочные работы. Некоторые принципы работы таких установок похожи, а другие отличаются в корне.
В среде аргона
Одной из разновидностей является автоматическая аргонодуговая сварка неплавящимся электродом. В качестве последнего выступает стержень из вольфрама с некоторыми добавками. Между ним и изделием возбуждается электрическая дуга, а аргоновый состав газовой смеси, подаваемый через сопло головки аппарата, не дает углероду вырываться через поверхность шва. Благодаря этому соединение получается крепким и ровным. Сварка в среде защитных газов может выполняться стационарно закрепленной головкой устройства, под которой изделие проворачивается, так и движущейся частью по линии соединения. Аргонно-дуговой метод активно применяется при работе с нержавеющими трубами и емкостями.
Порошковой проволокой
Еще одним вариантом является автоматическая сварка порошковой проволокой. Аппарат подает плавящийся электрод в зону сварки по роликам. Напряжение на конце проволоки создает дугу. Но для защиты расплавленного металла используется не порошок из бункера, а флюс, находящийся в самой проволоке. Для этого последняя изготавливается трубчатой формы и укладывается в бобины. Такой расходный материал стоит дороже, но облегчает подготовку к сварочному процессу. Сварочный станок не требует загрузки флюса в бункер. Наплавленный шов, как и в случае с насыпным порошком, нуждается в очистке. Аппараты могут работать перемещаясь на самом изделии или неподвижно, с прокруткой свариваемых частей под ними.
Плазменная сварка
Для быстрого соединения легированных сталей была разработана автоматическая плазменная сварка. В подобных устройствах электрическая дуга горит между двумя электродами в головке горелки. Аргон или гелий, подающиеся под высоким давлением и закрученный завихрителем, содействует ионизации пламени дуги, и усилению ее температуры. Плазменная сварка устанавливается на кронштейны, которые могут вращаться по оси. Расстояние от центра до головки может изменяться, что делает удобным это оборудование для круговых автоматических швов днищ емкостей. В зависимости от толщины металла и требуемой высоты шва, устройство может снабжаться дополнительным блоком подающим присадочную проволоку.
Кроме вышеперечисленных агрегатов встречаются их полуавтоматические версии, где сварщику требуется направлять сварочную головку или руководить движением трактора. Автоматическая и полуавтоматическая сварка востребованы не только на крупных предприятиях, но в небольших фирмах. Ведь таким способом можно значительно повышать производительность и доходность. Некоторые умельцы смогли сделать самодельный аппарат на основе полуавтомата, который способен передвигаться по заданной траектории.
3 Какие материалы используют для сварочных работ под флюсом?
От грамотного подбора электродной проволоки зависит качество сварки. Ее химсостав устанавливает механические параметры шва. Рекомендуется применять стальную проволоку, которая соответствует Государственному стандарту 2246-70. Изготавливают ее из легированной, низкоуглеродистой и высоколегированной стали. Диаметры готовой проволоки при этом стандартизированы, они варьируются в пределах от 0,3 до 12 мм.
Поставляется такая продукция обычно в 80-метровых (не более) бухтах, реже в кассетах либо катушках (требуется согласие потребителя). Перед использованием проволоки, хранившейся некоторое время на складах, профессионалы советуют производить ее очистку и специальную несложную обработку бензином или керосином, что позволяет удалить ржавчину и загрязнения с изделия.
Для сварки изделий из алюминиевых листов выпускают проволоку по стандарту 7871-75. Также часто применяют омедненную проволоку (ГОСТ 16130-72), которая не требует предварительной обработки перед сваркой. На условия протекания сварочного процесса и качество шва, конечно же, оказывает влияние и то, какой флюс был выбран. Его состав определяет характеристики газовой атмосферы и жидкого шлака. От взаимодействия последнего с металлом в свою очередь зависит и структура металла шва. А она обуславливает стойкость против формирования трещин.
Выбирая флюсы, стоит помнить, что они необходимы для:
Положительные и отрицательные качества
Автоматическая дуговая сварка под слоем флюса является востребованной технологией, которую активно применяют на производствах, предприятиях. При проведении этой технологии можно хорошо сэкономить на материале, при этом качество изделия никак не пострадает. Это осуществляется благодаря специальной эффективной конструкции, которая обеспечивает отличную тягу даже для компонентов с повышенной твердостью.
Автоматическая сварка под слоем флюса обладает целым рядом преимуществ:
- Данный вид сварки обладает повышенной степенью производительности. Она означает показатель метража шва, который производится за час работы дуги. Использование флюса повышает степень производительности сварки почти в 10 раз.
- За счет того во время сварочного процесса соблюдается стабильность и постоянная скорость прохода линии соединение имеет хорошее качество и высокую прочность.
- Закрытая дуга обладает высокой мощностью. Именно это способствует расплавлению металла на большую глубину в процессе сварочного процесса. Именно это избавляет от необходимости проводить разделку кромок под сварку. Но стоит учитывать, что открытая дуга не такая мощная, она требует предварительного разделывания кромок. Без этого условия невозможно получить хорошее сварное соединение.
- Главное преимущество данной технологии состоит в том, что весь процесс производится в автоматизированном режиме. Сварщик не обязательно должен уметь варить, ему достаточно знания того, как проводится настройка используемого оборудования.
- При выполнении автоматического сварочного процесса электрод применяется почти полностью, его потери составляют всего 2 %.
- Во время сварки не образуются брызги от расплавленного металла. Это приводит к экономии самого металла, что положительно отражается на стоимости и производительности сварочного процесса.
- Область сваривания отлично защищена от отрицательного воздействия воздуха и окружающей среды.
- За счет того, что во время автоматического сваривания применяются флюсы, происходит минимальное образование оксидов.
- На протяжении всего процесса наблюдается ровное пламя дуги. Именно за счет этого выходит прекрасная мелкочешуйчатая структура и сохраняется отличный эстетический вид сварного шва.
- От вредных внешних воздействий сварную область отлично защищает флюс. Во время сварки не требуется дополнительно применять специальные защитные устройства.
- Усиленное охлаждение металла после сварочного процесса приводит к образованию прочного и стойкого сварного шва.
- Этот метод обладает простым исполнением, для него не требуется иметь большой опыт, навыки.
Наличие большого количества плюсов делает сварку под слоем флюса востребованной технологией. Действительно этот метод пользуется широкой популярностью во многих областях производства, благодаря ему можно получить качественное и прочное соединение, которое способно прослужить длительное время. Кроме этого этот метод прекрасно подходит для сваривания трубных конструкций разного диаметра.
Но все не стоит забывать про то, что автоматическая дуговая сварка имеет негативные качества, среди которых можно выделить:
- сварка под флюсом, которая осуществляется в автоматическом режиме, является дорогим методом сваривания. Его может позволить далеко не каждый;
- во время процесса достаточно тяжело определить верное расположение материала для фиксации. Это связано с техническими характеристиками технологии;
- сварка может оказывать вредное воздействие на человека, который контролирует и выполняет весь рабочий процесс;
- для проведения процесса требуется дорогостоящее и редкое оборудование, которое имеется только на промышленных предприятиях. По этой причине данный вид сварки редко используется в бытовых условиях;
- перед проведением сварки требуется тщательная подготовка металла;
- не получится провести сваривание металл на весу. Деталь необходимо зафиксировать в горизонтальном положении и предварительно проварить корень сварного соединения.
Важно! При проведении автоматического сваривания сварочный трактор расплавляет часть порошка электрической дугой от проволоки, в результате этого появляется корка на поверхности шва. А другая часть порошка так и остается в виде гранул
После полного завершения процесса требуется очистить весь шлак.
Виды гранулированного порошка
Гост 1139-80. основные нормы взаимозаменяемости. соединения шлицевые прямобочные. размеры и допуски (с изменениями n 1, 2)
Для осуществления сварочного процесса, флюс подразделяется на несколько типов. Все зависит от металла, который будет обрабатываться:
- Высоколегированная сталь.
- Цветные сплавы.
- Углеродистая и легированная сталь.
Методика производства также подразделяет этот гранулированный материал на несколько подвидов:
- Керамический.
- Плавленный.
Использование первого вида позволяет получить улучшенный шов. Плавленый флюс отличается своей пемзовидной структурой.
Чтобы получить керамический материал, сначала специальные элементы подвергают мелкому измельчению. Затем смешивают с экструзией, которая помогает получить однородную массу. В нее добавляют жидкое стекло. Такая смесь используется только в том случае, когда требуется провести ещё одно легирование материала сварочного шва.
После спекания исходных веществ, проведения их грануляции, получается плавленый флюс. Гранулы для проведения газовой сварки делятся на несколько подгрупп. Разделение зависит от их химического состава:
- Солевые. В их состав входит большое количество хлоридов, а также небольшое количество фторидов. Гранулы применяются для сваривания активных металлов. Их используют для переплава оставшегося шлака.
- Смешанные. Материал представляет собой смесь солевых гранул с оксидами. Используется для работы с легированными сталями.
- Оксидные. Смесь предназначена для обработки фтористой стали или низколегированного металла. В состав входят окислы металла вкупе с минимальным количеством фтористых соединений.
Виды применяемых флюсов
Перед тем, как провести сварку под флюсом, неплохо было бы узнать, какие вообще бывать разновидности. Прежде всего, всю флюсы делятся по назначению. Они могут быть для сварки углеродистых и легированных сталей, для высоколегированных сталей и для цветных металлов
Это первое, на что стоит обратить внимание перед покупкой флюса
Также флюсы могут быть плавлеными или керамическими. Их отличие в составе. В большинстве случаев используется именно плавленый флюс, поскольку он относительно универсальный и стоит недорого. С его помощью можно эффективно защитить сварочную ванну от кислорода. Но не ждите от плавленого флюса каких-то особых качеств. Если вам необходимы действительно отличные свойства шва, то выберите керамический флюс. Он обеспечивает отличное качество.
Также флюсы могут быть химически активными и химически пассивными. Активный флюс содержит в составе кислоты, способные не только защитить металл при сварке, но и привести к коррозии. Так что тщательно удаляйте флюс после работы. Пассивные флюсы в автоматической сварке не применяются, поскольку не обладают достаточными для этого свойствами. Зачастую вы встретите пассивный вещества при пайке в виде воска или канифоли.
Кстати, о производителях. Это давний спор всех начинающих и опытных сварщиков. Кто-то считает, что отечественные компании производят недорогой и эффективный флюс, а кто-то всеми руками за импортные комплектующие. Мы не будем однозначно говорить, что лучше, скажем лишь то, что на практике и отечественные, и импортные флюсы показывают себя хорошо, если соблюдена технология сварки.
Полуавтоматическая сварка: принцип работы, видовое разнообразие
Сварочный аппарат состоит из следующих компонентов:
- горелка;
- шланг для подачи проволоки;
- механизм подачи проволоки;
- панель управления рабочими процессами;
- проволока в мотке;
- электропровод;
- система полуавтоматического управления;
- шланг для подачи газа;
- редуктор для снижения газового давления;
- нагреватель;
- баллон с газом высокого давления;
- выпрямитель.
На отечественном рынке присутствует большое разнообразие подобного оборудования. Дабы упорядочить его виды, обратимся к одной из наиболее распространенных классификаций. По мере автоматизации сварных процессов сварочные аппараты могут быть ручными, полуавтоматическими и автоматическими.
Первый тип подобного оборудования более подходит для бытового использования, а второй и третий – для применения на крупных предприятиях, так как сварочные автоматы, полуавтоматы отличаются более высокой производительностью за единицу времени, а также позволяют получить более качественные соединения металлов, нежели при работе ручным сварным агрегатом.
Но стоит заметить, что автоматические сварки стоят значительно дороже ручных агрегатов, поскольку характеризуются более высоким комфортом для пользователя, имеют широкие функциональные возможности, работают дольше.
Полуавтоматы выступают наиболее приемлемым вариантом по соотношению цены, комфортабельности работы и количества функций.
Чтобы понять иные достоинства полуавтоматов, нужно уяснить, как работает полуавтоматическая сварка:
- внутри аппарата находится катушка с проволокой, выполняющей функцию плавящегося электрода и автоматический механизм подачи такой проволоки;
- подвижная проволока пропускается через газовое сопло под напряжением, что приводит к ее расплавлению;
- стабильная длина дуги обеспечивается автоматическим механизмом подачи сварки;
- оператор выбирает на свое усмотрение направление тока и скорость подачи проволоки для сварки, учитывая вид металла и скорость перемещения газовой горелки.
Зависимость угла наклона горелки от толщины заготовки. Понимание принципа работы полуавтоматической сварки позволяет уяснить, чем отличается автомат от полуавтомата. В автомате абсолютно все процессы автоматизированы, то есть, выполняются системой управления. В полуавтоматических сварочных аппаратах, как было сказано выше, некоторые из операций остаются за сварщиком.
Полуавтоматическая сварка делится на разные виды, исходя из наличия определенных характеристик.
По способу защиты материала в процессе выполнения сварных работ различают полуавтоматы для сварки:
- под флюсом;
- в инертных и активных газах.
Также полуавтоматы могут быть:
- Однофазными. Функционируют от сети с напряжением в 220В, но если оно скачет, электрическая дуга не будет постоянной. Такое положение дел опасно появлению дефектов на сварных соединениях.
- Трехфазными. Функционируют не от каждой розетки, однако гарантируют высокое качество работы при любых нагрузках.
Основные режимы
От параметров проведения сварочных работ зависит итоговая форма и размер шва. Расположим их в порядке убывания влияния:
- Напряжение дуги.
- Величина тока.
- Скорость сварки.
- Диаметр электродной проволоки.
- Угол наклона электрода.
- Род и полярность тока.
- Тип флюса.
- Величина вылета электрода.
Проведение сварочных работ возможно при условии поддержания дуги. Таким образом, скорость подачи проволоки должна соответствовать скорости ее плавления в сварочной ванне. Изменение величины одного параметра должно сопровождаться изменением величины второго. При равном показателе силы тока проволока меньшего диаметра должна подаваться с большей скоростью. Влияние параметров режима на качество соединения изучают путем изменения одного из параметров, оставив прочие параметры неизменными.
Подбор режима сварки выбор проволоки.
Глубину проплавления металла можно увеличить путем повышения параметров сварочного тока. Соотношение данных параметров имеет практически линейный характер. С увеличением давления дуги расплавленный металл вытесняется интенсивнее. В результате повышается уровень взаимодействия между дугой и основным металлом. При этом ширина шва практически не увеличивается, поскольку дуга углубляется в основной металл.
Уменьшение диаметра электрода при постоянном токе повышает плотность сварочного тока. Подвижность дуги при этом падает, ширина шва уменьшается, а глубина проплавления увеличивается.
Изменения формы и размера шва можно добиться путем придания проволоке колебаний поперечных направлению шва. Амплитуда и частота подбирается индивидуально, в зависимости от требуемого результата. Метод применяется на автоматических установках.
Угол наклона электрода оказывает воздействие, аналогичное ручной дуговой сварке. Во избежание разбрызгивания расплавленного флюса, работы данным методом выполняют только в нижнем положении. Угол наклона изделия не должен превышать 15°. Практическое применение – соединение кольцевых стыков труб.