История станкостроения
Можно с уверенностью сказать, что все прототипы современных станков появились в период с 14 по 17 век. Так, в 1677 году в Туле была изготовлена сверлильная установка с конным приводом для рассверливания у пушки стволов. Русский токарь А. Нартов в начале 17 века создал не один токарный станок, экспонаты которых хранятся в музеях России и Франции. В 1714 году М. Сидоровым был изготовлен первый многопозиционный станок для сверления двадцати четырёх ружейных стволов одновременно.
В конце 18 века как отрасль промышленности в Англии появилось станкостроение. Её родоначальником считается кузнец Г. Модсли. Он открыл своё дело и на промышленной основе приступил к производству токарно-винторезных, сверлильных, долбёжных, расточных, фрезерных и других станков.
Первым станкостроительным заводом в России, построенным в 1790 году, был завод Берда. Находился он в Санкт-Петербурге. Но уже к 1913 году таких заводов было три.
В 1933 году приказом Наркомтяжпрома о развёртывании станкостроения положено образование станкостроительной промышленности как отрасли в Советском Союзе. СССР стал лидером мировой станкостроительной индустрии не только по количеству реализованных станков, но и по технологическому уровню. Всё изменилось после распада Союза, все связи между предприятиями, оказавшимися теперь в разных странах, были разрушены.
Обзор, посвященный исследованию мирового выпуска и потребления металлорежущих станков
Основной целью в конкурентной борьбе на мировом рынке по производству и продаже товаров обрабатывающей промышленности является увеличение производительности. Одним из способов увеличения производительности является использование более квалифицированного персонала. Еще одним способом увеличения производительности является использование более эффективного оборудования, такого, как, например, станки. Весьма легко посмотреть на эти два способа увеличения производительности, как на соперничающие; например, когда рабочий персонал против внедрения в производство роботов, либо иного, более эффективного капитального оборудования. Но на самом деле, более квалифицированный персонал и более эффективные станки дополняют друг друга. Следовательно, только сочетание этих двух составляющих ведет к повышению уровня жизни.
Способ объединения этих двух факторов зависит от их относительной стоимости. Последние годы наблюдался неуклонный рост квалификации работников на производстве по всему миру. Это способствовало улучшению качества обработки деталей по всему миру. Но более квалифицированному персоналу необходимо платить большие зарплаты и они должны получать и другие дивиденды. Одновременно на всем земном шаре наблюдается тенденция к небывалому понижению процентных ставок, что значительно снизило стоимость оборудования (основных средств). Динамика роста размера заработной платы и снижения процентных ставок означает, что в настоящее время можно сравнительно дешево увеличить производительность путем инвестирования в основные средства. Так как станки необходимы для эффективного производства всей выпускаемой продукции, уровень инвестиций в станки является показателем того, что страна, вкладывающая в обрабатывающее оборудование, смотрит в будущее и нуждается в квалифицированном персонале. В настоящее время тенденция закупок станков свидетельствует о том, что наиболее влиятельные страны-производители оборудования увеличивают инвестирование в новейшие технологии станочной обработки.
Мировое потребление станков в прошлые годы составляло $75.3 млрд.; в 2014 году наблюдалось увеличение на 0.3%. Но среди десяти крупнейших стран-потребителей станков, которые одновременно соответствуют 10 крупнейшим мировым экономикам, закупки станков в 2014 году увеличились на 1.7%. В 15 странах, которые, не являются основными мировыми лидерами по закупкам станков, потребление станков в 2014 году сократилось на 7.9%. Таким образом, страны с более сильной производственной базой больше инвестировали в потребление станков, что увеличило разрыв между ними и остальными странами.
Мировое производство станков три года подряд уменьшается и в 2014 году составило $81.2млрд. В 2014 году мировое производство станков сократилось на 3.1%. Доля сокращения производства в 2014 году замедлилась в связи с тем, что машиностроители понизили объем запасов (уровень незавершенного производства), приведя запасы (поставки оборудования) в соответствие со спросом. Это указывает на то, что мировые цены на станки должны увеличиться.
Смотря в 2015 год, обзор Gardner прогнозирует падение уровня затрат на станки на 0.4% до 75 миллиардов долларов США. Однако, 10 крупнейших потребителей уменьшат затраты на станки на 1.1% в то время как оставшиеся 15 крупных стран-потребителей увеличат потребление до 3.7%.
Мировое производство и потребление станков
Крупнейшие страны-экспортеры продукции машиностроения
Машиностроение стран лидеров приносит государственным бюджетам ощутимые капиталы. Например, доля стоимости продукции, реализуемая Соединенными Штатами, составляет 30% от всемирной. Япония продает товара на 15%. Германия около 10%. Менее успешны другие страны производители: Франция, Канада, Китай, Великобритания.
- США – 405 млрд долларов;
- Япония – 310 млрд;
- Германия – 302 млрд;
- Франция – 141 млрд;
- Великобритания – 138 млрд;
- Китай – 120 млрд;
- Канада – 105 млрд.
Страны-лидеры в некоторых отраслях:
- Автостроение – США, Япония, Германия, Франция, Южная Корея.
- Станкостроение – Япония, Германия, США, Италия, Китай.
- Тракторы – Россия, Япония, Индия, США, Беларусь.
- Телевизоры – Китай, Южная Корея, США, Бразилия, Малайзия.
- Судостроение – Южная Корея, Япония, Германия, Бразилия, Тайвань.
Судостроение в Японии
Главные страны, экспортирующие продукцию машиностроения:
- США;
- Япония;
- Германия;
- Великобритания;
- Франция;
- Италия;
- Канада;
- Корея.
Из развивающихся стран в этом списке:
- Китай;
- Тайвань;
- Сингапур;
- Индия;
- Турция;
- Мексика;
- Бразилия.
Некоторые факторы, влияющие на расположение станкозаводов в России
В Российской Федерации машиностроение относится к более важным в территориальном взаимоотношении в сфере промышленности. В одних регионах оно обладает профилирующей значимостью, но в иных его функции урезаны основным способом удовлетворения внутренних нужд.
1.Состояние экономики и уровнем развития области.
2.Множество станкостроительных фирм открываются в тех регионах, где она наиболее важны. В таком случае данные регионы, как правило, считаются достаточно емкими покупателями данного продукта. Поэтому источники сырья с зонами пользования продукта – наилучший вид размещения машиностроительных компаний. В данном случае существенно уменьшаются автотранспортные затраты по транспортировке материала, машин и оснащения.
Из числа условий, оказывающих большое влияние в расположении, существенная роль заключается в квалификации, также кооперированию изготовления.
3.Квалификация представляет собой крупные способности с целью применения очень эффективного производственного оснащения, также средств автоматизации производственных процессов.
4.Квалификация непосредственно сопряжена с кооперированием, что подразумевает собой содействие в ходе изготовления продукта несколькими предприятиями.
5.Наукоемкость. Изготовление более современной также непростой техники, где имеются высокоразвитые научные центры. Направленность на научный потенциал — главное условие размещения машиностроительных компаний.
6. Трудозатратность – крупные расходы и значительная высокая квалификация труда. Изготовление требует весьма крупных расходов трудового периода, поэтому сфера машиностроения склонна к регионам, с значительной концентрацией жителей.
7.Металлоемкость. Продукция потребляет существенную долю черных и цветных металлов.
8.Миграционный прирост. Основной поток людей мигрируются туда, где уровень жизни наиболее благополучен. Поэтому там больше возможности предоставить более оплачиваемую работу и высокую зароботную плату.
9.Распространение новых технологий и формирование новых технологических укладов, которые очень быстро могут обесценить существующие производства
Описание:
Станком обычно считается оборудование с механическим приводом, не требующего всех перемещений вручную, источником энергии для которого служит внешний источник энергии. Данное оборудование было специально разработано для обработки металлов резанием, для обработки металлов давлением (металлоформующие), физико-химической обработки, либо для комбинированной обработки.
Все станки традиционно подразделяются на две категории: металлорежущие и станки для обработки металлов давлением. Металлорежущие станки обычно выполняют обработку металлов со снятием стружки или металлических опилок. В данную категорию станков входят (но не обязательно только перечисленные типы) протяжные станки, сверлильные станки, электроэрозионные станки, лазерные станки, зуборезные станки, шлифовальные станки, обрабатывающие центры, фрезерные и токарные станки.
Станки для обработки металлов давлением обычно выполняют сжатие/деформацию металла с приданием ему формы. В эту категорию станков входят (но не обязательно только перечисленные типы) гибочные прессы, холодновысадочные пресс-автоматы, прессы, ножницы, агрегаты продольной резки рулонной полосы, штамповочные прессы. Данные, представленные в WMTS, верны только для металлорежущих станков (коды 8456-8461 в Гармонизированной системе описания и кодирования товаров) и для станков, предназначенных для обработки металлов под давлением (8462-8463) и действительны только для окончательной обработки; в эту категорию не входят запчасти и модернизированные станки.
Обменный курс:
Все данные отчета, поступающие по каждой стране в национальной валюте, конвертируются в доллары США с использованием среднесуточного курса обмена валют, как сообщается на www.oanda.com в разделе истории. Вся аналитика осуществляется в долларах США.
Проблемы отрасли
Кризис российского станкостроения, пик которого пришелся на 90-е годы прошлого столетия, имеет системный характер, а его причины во многом актуальны и сегодня. Разберем подробнее:
Технологическое отставание.
Производство станков и оборудования – сложный технологический процесс, обеспечение которого требует значительной материальной и кадровой основы
Кроме этого, важное значение имеет развитый спектр НИОКР
После распада СССР материальные ресурсы в развитие станкостроения практически не вкладывались. В этой связи технологии производства станков и оборудования в России во многом устарели.
Низкая конкурентоспособность.
Продукция отечественного станкостроения, как правило, менее технологична, чем зарубежная. Кроме этого, российские производители сталкиваются с высокими издержками, связанными с практически полным отсутствием государственного субсидирования и дешевых кредитов. В этой связи стоимость продукции отечественных производителей весьма высока.
Сужение рынков сбыта.
Болезненный переход к рыночной экономке привел ко значительному спаду всех отраслей народного хозяйства в стране. На этом фоне продукция российского станкостроения в период кризисных явлений 90-х годов оказалась невостребованной на внутреннем рынке. На внешних же она не смогла выдержать конкуренции с зарубежными производителями. Оживление, произошедшее в промышленности в 2000-е годы, затронуло станкостроение лишь отчасти, поскольку российские промышленники предпочитали работать на иностранном оборудовании. На данный момент доля соответствующего импорта также остается весьма высокой.
Мировые тенденции
Последние двадцать лет ознаменовались мировым увеличением потребления станков в 3 раза, а производство достигло отметки в сто миллиардов долларов. В мире наибольшую долю в производстве станов занимает Азия, на втором месте Европа, на третьем Северная и Южная Америка.
Лидером станкостроительной промышленности является Китай, который в 2014 году потеснил с лидерских позиций Японию и Германию. В Китае сосредоточены производственные мощности производителей автоматики, гидравлики и числового программного управления.
Совместный бизнес с проведением скоординированной политики ведут компании Германии и Японии. Они обмениваются маркетинговыми и инженерными ресурсами, организуют совместные выставки, под одним брендом осуществляют производство станков.
В мире нет стран, которые можно назвать чистыми экспортёрами или импортёрами станков. Какую-то часть продукции страна производитель потребляет сама, другую экспортирует. В Германии, Италии, Японии производство станков занимает больший удельный вес, чем потребление. Лидерство по поставкам занимает Китай, на втором месте Германия, следом идут Италия, США.
[править] География
В 2000 г. на Западную Европу приходилось от 40 до 50 % мирового спроса на продукцию станкостроения, на страны Азии — около 25 %. С тех пор это соотношение коренным образом изменилось. К 2012 г. доля Европы упала до 25 %, в то время как на страны Азии пришлось две трети мирового спроса. Эксперты предсказывают углубление этого тренда. Высокими темпами будет расти спрос в России, Индии, а также Бразилии и других латиноамериканских странах. Перспективными регионами являются Турция и Северная Африка. Развитые же страны, в том числе США и Япония, продолжат терять свои позиции.
Выделяется по размерам станкостроение Китая. Однако здесь упор пока делается на производстве оборудования среднего уровня качества и точности. Оно поставляется предприятиям, находящимся на нижних уровнях цепочек добавленной стоимости. Китайское правительство прилагает активные усилия для совершенствования своего станкостроения, постоянно увеличивая затраты на НИОКР. Импорт станков в страну ограничивается только теми видами, которые не могут быть произведены на территории Китая. Для китайских компаний, стремящихся инвестировать в комплексные системы оборудования, поставляемые из-за рубежа, существенно ограничивается доступ к финансовым источникам. Иностранные экспортеры отмечают заметное ухудшение условий ведения бизнеса по сравнению с предыдущими годами, когда импорт современного оборудования поощрялся китайскими властями в целях повышения технического уровня отраслей обрабатывающей промышленности. Аналогичные тенденции наблюдаются в Бразилии и Аргентине.
Как превратить иностранный товар в Made in Russia
Со времён СССР выпуск металлорежущих станков в стране упал в десятки раз. А доля наиболее высокотехнологичных — с числовым программным управлением (ЧПУ) сегодня составляет около 10%, сказано в отчёте Евразийской экономической комиссии (ЕЭК). По производительности и точности российская продукция пока сильно уступает немецкой, японской, американской, итальянской и китайской.
Зарубежные станки практически полностью вытеснили отечественные, а создание современного оборудования без иностранной начинки технически невозможно. Об этом говорят данные ЕЭК за 2017 год: экспорт составил $71,9 млн при импорте более $1,9 млрд.
Критическая ситуация на рынке привела к переходу бизнеса на «серые схемы» и приклеиванию этикеток на зарубежные комплектующие. Так, разработанные и завезённые в РФ узлы получают статус Made in Russia
Крупные госкорпорации заинтересованы в поставках качественных товаров, при этом им не важно, где они сделаны. По документам Минпромторга отечественные изделия пользуются спросом. Фактически же в России часть весьма крупных по местным меркам компаний производит станину, модернизирует старое советское оборудование и выдаёт за новое
Фактически же в России часть весьма крупных по местным меркам компаний производит станину, модернизирует старое советское оборудование и выдаёт за новое.
Павел Лисицын/РИА Новости
Свою роль в «превращении» иностранных машин для обработки металла в российские сыграло и игнорирование мнения бизнеса. Предприятия не спросили, сколько времени понадобится на изготовление станка с высокой долей локализации в РФ.
Пункт № 1 постановления, о котором говорит директор, определяет критерии, подтверждающие производство продукции на территории РФ. Один из них — акт экспертизы от Торгово-промышленной палаты РФ.
Однако схема «Китай — Made in Russia» весьма популярна, рассказали на рынке. Ранее компании старались скрыть такой факт и заявляли о собственных площадках в КНР. На деле же им строят в Китае цех, а они завозят в РФ изделия прямо с иероглифами.
История развития отрасли в России
Необходимость в специальных машинах, которые бы применялись в производстве, возникла в момент промышленной революции одновременно с появлением крупных предприятий заводского типа. В Российской империи это время приходится на конец XIX века. Однако станкостроение как отрасль отсутствовало, поскольку государство оставалось аграрным.
Развитие уже советской промышленности требовало современных средств производства. На протяжении 20-х и начала 30-х годов правительство СССР активно закупает станки иностранного производства, проводя политику индустриализации государства. Параллельно с этим создаются и отечественные предприятия.
Производство станков и оборудования получило наибольшее развитие в послевоенные годы, когда растущая индустрия СССР остро нуждалась в средствах производства. По стране создавались сотни заводов, продукция многих из которых не имела аналогов за рубежом. К началу перестройки Советский Союз стал одним из лидеров мирового станкостроения.
После распада СССР отрасль, как и все народное хозяйство страны, оказалось в глубоком кризисе. Производство сократилось в десятки раз, по многим позициям технологии и вовсе оказались утраченными. Небольшое оживление произошло только к концу первого десятилетия XXI века, однако связано оно с возросшими потребностями отечественного ВПК.
Производители станков
Китай остается крупнейшим в мире производителем станков, начиная с 2009 года. Но производство сократилось до $23.8 млрд по сравнению с пиком в $29.5 млрд в 2011 году. Природа китайского рынка производителей станков и охлаждение темпов роста экономики позволяет предположить в 2015 году некоторый спад в производстве китайских станков.
В течение нескольких лет Германия находилась на втором месте по производству станков. Однако в 2014 году производство сократилось примерно на 20%. В то же время страна является крупнейшим в мире экспортером станков.
В Японии производство станков упало с 2011 года по 2013 год почти на 50%. Но в 2014 году производство быстро восстановилось, увеличившись до $12.8млрд. Это поставило Японию на третье место в мире с отставанием от Германии всего на $0.1млрд.
Южная Корея поднялась на одну позицию и заняла четвертое место, в то время, как Италия опустилась на одну позицию и занимает пятое место по производству станков. Эти две страны произвели станков на общую сумму более $5 млрд.
С 2011 года, также как и с 2007 года производство бразильских станков переживает драматические моменты. Начиная с 2011 года производство станков в Бразилии упало почти на 70% с $0.3млрд до $0.9 млрд долларов.
Кому достался пирог
В 1938 году, когда мир уже предчувствовал Вторую мировую войну, станкостроительных держав было четыре. Лидерами были США и Германия, за ними в четверку входили СССР и Великобритания. В 1970-х годах Великобританию вытеснила Япония. Ситуация за 80 лет значительно поменялась – Штаты сражаются за место в семерке лидеров с Тайванем, поскольку их доля в мировой торговле станками 5–6 процентов, как и Тайваня. России, наследницы СССР, в семерке лидеров нет.
Объем продаж на глобальном рынке, по данным Gardner Research, сегодня превышает 90 миллиардов долларов, при этом темпы прироста мировой станкостроительной отрасли последние 20 лет превышают в среднем 4 процента в год. Для отрасли характерно соотношение, при котором 56,2 процента всей продукции выпускают 3 страны – КНР, Япония, ФРГ. Далее идут США, Корея, Великобритания Франция.
Сегодня основным рынком стал Азиатско-Тихоокеанский регион, считает эксперт Центра развития ВШЭ Александр Бутов. И основную роль играет Китай, с 2002 года мировой лидер потребления станков. С 2009-го на долю Пекина приходилось не менее 33,7 процента от общемирового объема продаж данной товарной группы, а в потреблении станков – до 31,4 процента. Аналитики полагают, что китайский рынок определяет отраслевую динамику в мире.
Второе место в потреблении продукции станкостроения среди макрорегионов удерживает Европа. Причем немецкая промышленность обеспечивает более половины экспорта ЕС за рубеж.
Основной объем мирового рынка станков сосредоточен всего в трех регионах: АТР, Западной Европе и Северной Америке, где ситуация определяется уровнем потребления США.
Лидеры станкостроительной индустрии используют различные инструменты поддержки финансового и нефинансового характера:
- прямое денежное вливание;
- налоговые льготы;
- специальные ставки амортизации;
- льготное долговое финансирование, подготовка кадров и прочие преференции.
Фото: blogspot.ru
КНР – крупнейший потребитель станков, однако в 2018 году продажи на китайском рынке снизились с 30,7 до 28,8 миллиарда долларов, а доля в мировом потреблении упала до 31,4 процента.
Наиболее передовыми в техническом отношении являются станкостроительные корпорации Trumpf (ФРГ), Amada (Япония), Haas (США). Впереди не только промышленные гиганты вроде Китая и США, но и Австрия, Испания, Бразилия.
Кто станет в будущем абсолютным мировым лидером, сложно определить. В КНР, развивая народное хозяйство, изначально стремились добиться независимости от чужих технологий, и многого достигли. При этом китайцы делают упор на выпуск сложнейших автоматизированных, с компьютеризированным управлением, промышленных станков.
Итак, вместе с Китаем в тройку мировых лидеров производства и экспорта станков входят Япония и ФРГ, далее с отставанием (раза в два) следуют США, Южная Корея, Италия, Тайвань, Швейцария. Доля остальных стран составляет менее одного процента.
Одновременно Пекин, Вашингтон и Берлин возглавляют список не только экспортеров, но и импортеров станков. Ведь при современном производстве узкоспециализированных агрегатов даже для развитой страны рентабельнее купить особо редкие станки за рубежом, нежели тратиться на их разработку и производство. Кроме того, лидеры мирового станкостроения переформатировали отрасль так, что выпуском наукоемких комплектующих занялись локальные центры компетенций. Так, электрошпиндели выпускает одни, револьверные головки – другие, шарико-винтовые передачи – третьи, системы ЧПУ разрабатывают четвертые фирмы. В итоге предприятие на последнем этапе только собирает станок из готовых деталей. Среди поставщиков ЧПУ выделяются страны, традиционно лидирующие в производстве высокотехнологичного оборудования: Япония, ФРГ, США. Российские производители здесь проигрывают в надежности изделий, что ведет к дополнительным издержкам у потребителей наших систем при ремонте и наладке.
История станкостроения в России
До реформ 2000 года подавляющее большинство станкостроительных компаний жили «чудом», чтобы увеличился спрос на их продукт. После того, как производство снижалось из года в год в период «перестройки» за несколько лет упала производительность станков в 2 раза больше.1998 год — уменьшилось изготовление больше чем в 10 раз, достигли 7590 единиц производства. Эквивалент падения более чем в 30 раз, с 3,3 млрд. долларов до 100 млн. долларов. 2000 год — самый успешный год для станкостроителей за последнее десятилетие. По сравнению с 2000-2001 годом производство в 2002 году снизилось еще на 25%. В данный период станкостроение отражает чрезвычайно сложное состояние отрасли. В дальнейшем этот спрос сохраняется.
В первой половине 2003 года появились глубокие проблемы в российской промышленности, отсутствие потенциала в возможности превратить тенденцию расширения в плотный путь развития. Начатая работа в Правительстве переоснащать и развивать станкостроение. В 2011 году было 46 производителей металлорежущих станков, 25 заводов кузнечного оборудования и 29 производителей режущего, измерительного и сборочного инструмента, семь научно-исследовательских институтов и 45 конструкторских бюро.
К 2012 г. пришлось списать половину техники. Если в 2006 г. в Российской Федерации работали в общей сложности 1,5 млн станков, то в 2012 — семьсот тыс. Подобным способом, объемы производства критически уменьшились — в десятки. Причем произошло это как за счет сжатия внутреннего рынка, так и в связи с потерей экспортных возможностей, где традиционная советская ниша была занята китайским товаром. В настоящее время в россии рыботают около ста станкостроительных предприятий. Изготовление станков в 2015г. перевалил 7.8 тыс. единиц. На фоне мирового рынка это менее 0,5%. Моральная и физическая изношенность основных фондов в российском машиностроении очень высока. В последние годы она только увеличивается. Благодаря принятым мерам с начала действия программы по импортозамещению в 2014г. доля импортного оборудования сократилась. По словам премьер-министра Российской Федерации Дмитрия Медведева, в 2017 г. она снизилась до 70%, хотя еще недавно составляла 87%.
В 2011 г. Правительство приняло госпрограмму развития станкостроения, расчитанную до 2016г. Тогда государство пообещала потратить 26 млрд. рублей на разработку станков всемирного уровня также создание линий с целью их изготовления. Но после принятия спрос и затраты на металлорежущее оборудование в России постоянно возрастали.2011 году Российская Федерация взяла 21-е место в мире по изготовлению станков. В 2012 году в стране было произведено 3321 металлорежущих станков помимо этого 4270 деревообрабатывающих станков. В 2013 г. стовосемьдесят компаний, вступающих в ассоциацию «Станкоинструмент», изготовили на 26,6 млрд. руб.. Основным инвестором в кластере — «MTE Koвосит МАС» общественная организация, образованное русской командой MTE и чешской группой Kovosvit MAS в июле 2012 года. Эта организация бфла единственной в Европе, которая производила токарные, фрезерные и другие машины.
В 2014 г. структура наименований продуктов, выпускаемых российскими станкостроительными фирмами, претерпела большие перемены, характеризующиеся увеличением изготовления оснащения с управлением также обрабатывающих центров, что повергло к увеличению доли сверхтехнологичной продукции, также показали серьезное воздействие в научно-технические движения. В 2015 году в рамках компании «Станкоинструмент» производственная мощность согласно выпуску станков добились 1873 единиц. Это 172,8% от уровня 2014 года.
Одним из значимых отраслевых событий в 2015 г. было развитие основного индивидуального раздела станкостроения СТАН, в состав которого вступают активы крупнейшей российской фирмы, в этом же количестве сферы нелегкого машиностроения. В марте 2016 года в Екатеринбурге существовало свободно отечественное и японское массовое изготовление 120 станков с ЧПУ с годовой эффективностью. Станкостроительная область не в состоянии обеспечить потребности внутреннего рынка, поскольку ей не хватает нового, современого, качественного оборудования для эффективного производства. Даже в благополучном 2014г. Производство металлорежущих станков едва дотягивал до четрырех тысяч штук, деревообрабатывающих станков — до пяти тысяч, т.е. реальные показатели были хуже, чем в 200г.
Отрасли машиностроения
Отрасли машиностроительного производства разделяют на три группы:
- общее машиностроение;
- транспортное машиностроение;
- электротехническое машиностроение.
К общему машиностроению относится тяжелое машиностроение, атомная сфера, производство сельскохозяйственного оборудования и другие. Разнообразие продукции – оригинальная черта этой отрасли.
Транспортное машиностроение разделяется на несколько узкопрофильных отраслей, среди которых автомобилестроение, судостроение, авиаракетно-космическая промышленность, производство ж/д оборудования. Транспортное машиностроение имеет как гражданскую направленность, так и военную.
Ростех – за станком
В 2020 году правительством страны была принята «Стратегия развития станкоинструментальной промышленности на период до 2035 года», в которой было отмечено, что текущий объем производства металлообрабатывающего оборудования покрывает лишь 17% внутреннего спроса. Справедливости ради можно отметить, что в 2016 году этот показатель составлял лишь 8%. Вклад станкостроения в валовый внутренний продукт составляет 0,02%, что в разы ниже показателей основных стран-лидеров по производству станков: Китая (0,15%), Японии (0,23%), Германии (0,32%).
При этом спрос отечественных предприятий на высокотехнологичное оборудование растет, особенно с учетом перехода на новый технологический уклад и цифровизацию производства. Сейчас, когда импорт иностранного промышленного оборудования ограничен, развитие собственных производителей станкостроительной продукции входит в список ключевых задач страны.
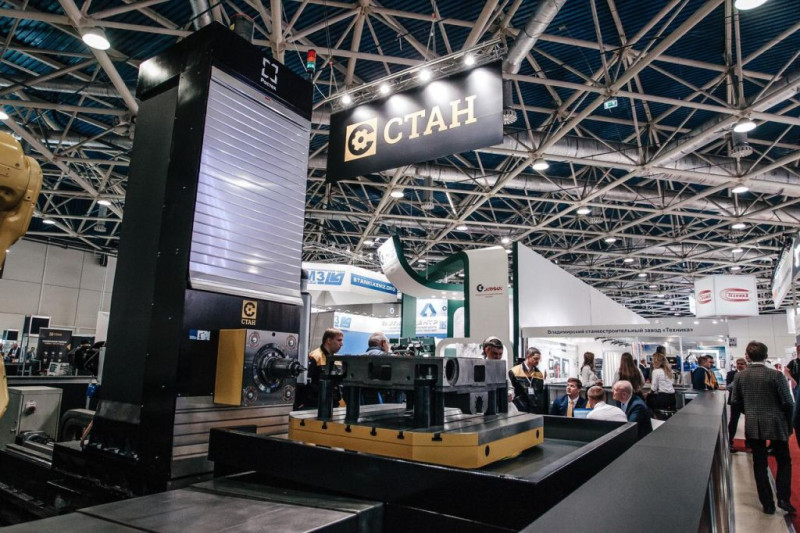
Фото: компания «СТАН»
В «Стратегии развития станкоинструментальной промышленности на период до 2035 года» рост производства станкоинструментальной продукции планируется со средним темпом на уровне 5,7% в год, до уровня 79,5 млрд рублей к 2035 году. При этом увеличение уровня локализации российской продукции отрасли должно вырасти до 70% за счет развития отечественного производства ключевых высокотехнологичных комплектующих.
Воплощать эти планы на практике поможет новая инициатива Ростеха – создание холдинга со специализацией в области разработки и производства тяжелого обрабатывающего оборудования и инструмента для промышленности. Новый холдинг объединит существующие станкостроительные активы Ростеха: «Станкопром» и его дочерние организации, НИТИ «Прогресс», и некоторых других производителей отрасли. Единая структура поможет оптимизировать производственные процессы, сконцентрироваться на разработке новых технологий в станкостроении. К 2030 году объединенная станкостроительная компания намерена занять до половины российского рынка промышленного оборудования.
Как зовут автора статьи и когда её выпустили ? Хочу использовать вашу статью как основу к своей научной статье